Casting replacement knobs
|
|
|
|
Location: Wangaratta, VIC
Member since 21 February 2009
Member #: 438
Postcount: 5254
|
Sniffing glue may get you into trouble: To me that is something that could be cut out of a perspex
|
|
|
|
Location: Wangaratta, VIC
Member since 21 February 2009
Member #: 438
Postcount: 5254
|
This looks to me like something that could be made from Perspex Rod and the hole drilled.
Marc
|
|
|
|
Location: Canberra, ACT
Member since 23 August 2012
Member #: 1208
Postcount: 584
|
I've started following Scraps' method (see post #7 above) and got as far as embedding the model knob in the mould silicone/shellite mixture in a small disposable plastic tub with about 1cm of the mould mixture on the sides, about .5cm on the bottom.
Now I'm a bit concerned about how long this will take to cure. Once the top of the mould has formed a silicone skin, the body of it becomes increasingly airtight so the rate of cure must slow down as there is less exposure to oxygen.
With about 3mm skin on top, I've taken the step of carefully tipping the mould mass out of the container, like taking a jelly out of its mould, so it's now sitting the other way up on the cured side, with all the surfaces exposed to the air. With a knife blade I could work the uncured silicone surface back into shape, to the extent it had moved during the tipping process.
Interested to know Scraps' or others' experience in how long to expect silicone to take to fully cure. I've had a few tubes fully cure themselves behind my back while on the shelf, but that was probably over a period of years.
Maven
|
|
|
|
Location: Blue Mountains, NSW
Member since 10 March 2013
Member #: 1312
Postcount: 401
|
I usually put them aside for a few days and find something else to work on, as hard as that may be 
|
|
|
|
Administrator
Location: Naremburn, NSW
Member since 15 November 2005
Member #: 1
Postcount: 7301
|
Most silicone products have a short shelf life. They will work beyond that up to a point but texture and bond do weaken with age, even when still inside an unopened tube. Bunnings and Masters know this yet still fill a whole aisle with more silicone than they can sell in a year whilst being just about out of stock with other essentials.
All Clear and similar products are useless for the type of application we are discussing here. This is almost completely lacking in flexibility and even when used for what it was intended for, it hardens in the sun and turns a transparent orange colour within a year.
Sikaflex is a better product than regular silicone sealants however it is much more expensive.
‾‾‾‾‾‾‾‾‾‾‾‾‾‾‾‾‾‾‾‾‾‾‾‾‾‾‾‾‾‾‾‾‾‾‾‾‾‾‾‾‾‾‾‾‾‾‾‾‾‾‾‾‾‾‾‾‾‾‾‾‾‾‾‾‾‾‾‾
A valve a day keeps the transistor away...
|
|
|
|
Location: Blue Mountains, NSW
Member since 10 March 2013
Member #: 1312
Postcount: 401
|
I've found just a pure silicon works best, nothing fancy, just the cheap stuff. The only difference I found is the time it takes to go off. Some set within a few hours and others take days. From what you say Brad the ones that go off quickly might be older stock.
|
|
|
|
Administrator
Location: Naremburn, NSW
Member since 15 November 2005
Member #: 1
Postcount: 7301
|
That may be the case though there's so many types of silicone and its made by about half a dozen different manufacturers so it's not a hard and fast (no pun intended) rule.
‾‾‾‾‾‾‾‾‾‾‾‾‾‾‾‾‾‾‾‾‾‾‾‾‾‾‾‾‾‾‾‾‾‾‾‾‾‾‾‾‾‾‾‾‾‾‾‾‾‾‾‾‾‾‾‾‾‾‾‾‾‾‾‾‾‾‾‾
A valve a day keeps the transistor away...
|
|
|
|
Location: Canberra, ACT
Member since 23 August 2012
Member #: 1208
Postcount: 584
|
Further to Scraps' recipe and GTC's links, I have found few sources for different ways to make a mould using silicone. The two below feature very fast-curing recipes using household materials and common clear silicone.
1.
Silicone Mould from household materials
uses corn starch as a stabiliser and water-absorbent that seems to result in a fairly rigid mould - you would press your model knob into the material while it is still malleable (if it is a suitable shape) or make the two-part mould, if necessary for more complex shapes, as demonstrated for a full 3D cast. Maybe this could be adapted for knobs with odd profiles such as long stems. A channel would need to be left to what would be the top of the finished 3D mould, to pour in a resin in liquid form, analogous to metal casting or injection moulding.
2.
Worlds easiest silicone mould
uses a strong dishwashing detergent solution with glycerine content as catalyst, to wet-cure common silicone into a dough-like consistency that can be wrapped around the object to be cast, and later peeled off as the mould.
More experiments ahead...
Maven
|
|
|
|
Location: Tamworth, NSW
Member since 6 April 2012
Member #: 1126
Postcount: 466
|
I think that in the next few years, with the price of 3d printers falling, this will be a viable option for making knobs and other assorted parts.
I am however following this thread closely as I have a broken knob on a set that no one yet has been keen to attempt a repair on.
ben
|
|
|
|
Location: Canberra, ACT
Member since 23 August 2012
Member #: 1208
Postcount: 584
|
Agree 3D printers OUGHT to be a solution, once price is in reach. Other problem is you need a 3D CAD model to feed to the 3D printer, so either a 3D scanner or the skills to create a virtual model from measurements, before the 3D printer can reproduce it.
Maven
|
|
|
|
Location: Wangaratta, VIC
Member since 21 February 2009
Member #: 438
Postcount: 5254
|
I find it amazing that there is experimenting when, a moulding compound can be bought off the shelf & tried.
What knob broke where...... more info. Ones with hollow backs are easy but, if the plastic has started to decompose you are in the poo.
The brass end of a spent shotgun shell packed with "kneed it", or machinable type, is handy to make a temporary knob for an external & some internal shaft types.
Marc (Farmer).............Recycle
|
|
|
|
Location: Canberra, ACT
Member since 23 August 2012
Member #: 1208
Postcount: 584
|
Well I tried each of the methods and staggered towards a conclusion that suits me - others may have other priorities.
The main problem with both silicones and resins is getting the curing process right. I did not get good results with the pure silicone/shellite/glycerine mixture, but that may have been due to my incompetence or perhaps frosty overnight conditions in Canberra.
1. Mould: I had best results using the silicone/starch moulding compound.
40% generic clear silicone
40% household starch
10% Shellite
Used the bent-nail-in-drill-chuck mixing method - worked very well
Pros: sets very quickly to consistency of wet dough, so knob can be pressed in. Cures solid in a few hours to a clean, non-tacky mould that is firm but can flex. Can hold fine detail.
Cons: The mould will continue to shrink up to 15% if left empty so can't be re-used.
It is advisable to use the mould more or less immediately you remove the model from it. It seems not to shrink while the compound is in it.
Over several attempts, it worked best when I brushed the model knob with vegetable oil, then buttered it with wet mould compound, immediately after mixing. This avoided accidental bubbles being caught while pushing the knob into the hardening compound.
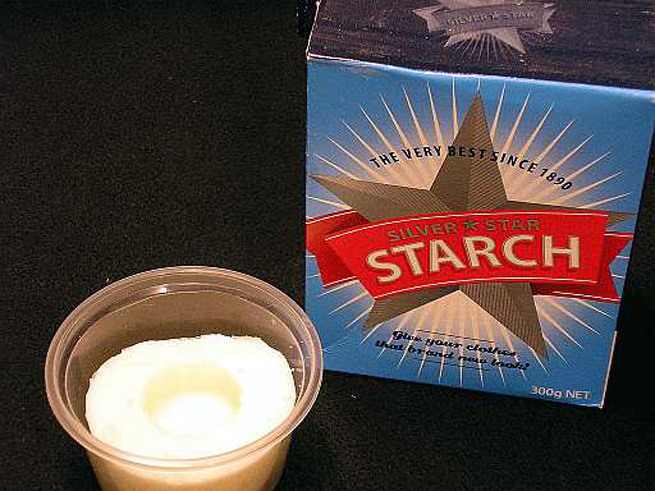
2. Cast:
I used the Diggers product.
Pros: It is relatively cheap so you can experiment without too much regret. While semi-cured, it can be sawed and drilled quite easily. It is initially the viscosity of honey and will take up all fine detail from a mould.
Cons: The catalyst is highly concentrated and measured in drops, so it can be difficult to get the mixture right. Colour has a slight green tinge when cured, so is not a perfect match for a clear plastic knob.
If not enough catalyst is used, the compound can cure very slowly. It sets hard enough to take out of the mould within 24hours, but then remains slightly malleable and tacky for a few more days. I got one or two attempts out of shape before realising that. Also can get a cloudy surface if handled before fully hardened. I would recommend adding catalyst at the high end of the instructed amount.
Also, due to the shrinkage issue, I found it best to build up a 2mm dam of the mould compound above the level of the model knob, so that the casting compound could be poured in proud of final desired shape. An earlier attempt shrank down into the mould too far. It's easier to take off than add to the final result.
The left channel volume control knob is a good match in dimension and detail, though colour match is not perfect (the close-up photograph exaggerates the green/gold tinge due to local lighting - lower photo is better). On the tuning dial knob, I had no model. The disk is salvaged perspex. I separately cast the top of the knob and also a boss for the stalk of the knob, as this needs to protrude down below fascia level to mate with the tuning condenser axle. I didn't attempt to imitate the knurling on the outside of the disk, so just gave it a ring of gold paint.
The hardest thing to match is the faded metallic discs on top of the knobs. I have used the nearest colour I could find in craft paper, glued and lacquered. If I find something closer to the original metal, I will replace it.
In position, the knobs are functional and probably as close as my limited skills will get me to a complete match.
The lifting hook on the tone arm is also a replacement for a missing original. This is made from one half of the kind of double-sided hasp you use for securing a blind cord.
Maven
|
|
|
|
Location: Australia, SA
Member since 21 December 2011
Member #: 1047
Postcount: 85
|
Years ago we used a drying oven to cure araldite, it goes into a very runny state so make sure it is welled up so it cannot run out of the joint and onto the floor.
|
|
|
|
Location: Newcomb, VIC
Member since 24 May 2015
Member #: 1750
Postcount: 7
|
Seems to me that knobs and similar small plastic parts would be perfect target for a 3D printer.
These machines are getting cheaper and better, and I've been thinking of getting one.
cheers,
Bernie
|
|
|
|
Location: Sydney, NSW
Member since 28 January 2011
Member #: 823
Postcount: 6687
|
Yes, I expect that 3D printers will eventually be like laser and inkjet printers where the device is comparatively cheap to buy, but then you get ripped off with supply stock.
|
|
|
You need to be a member to post comments on this forum.
|